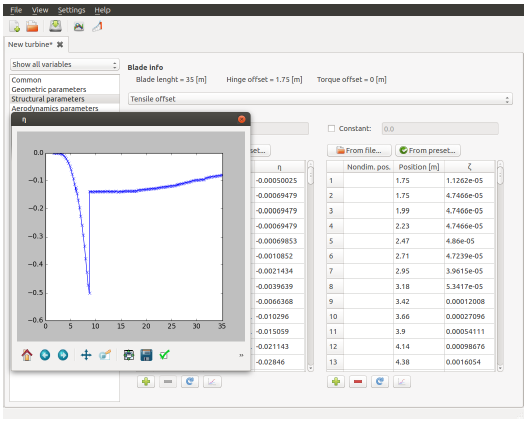
Enhancement of an Aeroelastic Solver for Design Optimization of HAWT
University Roma Tre (hereinafter UR3) Rotorcraft group, on behalf of AirWorks Engineering (hereinafter AW), developed and improved a code for HAWT’s aeroelastic optimization during the period September-2013/June-2014,.
Technical Note to be deliverd to POR-FESR board.
The final goal of the work was the enhancement of the aeroelatic-design
optimization tool developed in the previous years. The aim was to improve both the availability and the quality of the aerodynamic models, of the bladebox modeling, and of the optimization criteria, in order to be more useful and a more direct aid in the preliminary-design phase of HAWT blades layout.
Furthermore, the solver has been given a GUI, currently at its Beta-Version, to be usable from a common user in a friendly way.
UR3 and AW cooperated to assemble such a tool as follows in brief:
- The aeroelastic module provided by UR3, namely Tiltaero (TA), was enhanced with more aerodynamic modeling capabilities, apart from AW’s Aerodyn (Adyn) module, providing the user a set of choices depending on the desired analysis. The former data files required from TA and Aerodyn were of course merged or substituted to be suitable for every chosen model.
- AW developed both a structural model of the blade-box and a tool for the sectional structural strenght analysis. In general the bladebox model provides the sectional properties necessary for the aeroelastic analyses starting from real design values, like internal thicknesses, spar width and cells number.
- A new solver was assembled, named AEP (Annual Energy Production), able to use TA to compute a power curve and the following AEP for a HAWT with assigned nominal power, RPM and a given wind speed statistic distribution, with a given regulation strategy (pitch or stall).
- The design optimization tool (MDO) was integrated and enhanced with the new and the enhanced modules, thus changing the overall design process in terms of constraints, design variables and objective functions.
- UR3 designed and developed a GUI to access both to separate performance and structural analyses capilities of TA, and to use the design tool.
Please find out more on the article full version available for download in the download section.